Hoxe en día existen tres tipos de vidro plano no mundo: o estirado plano, o método flotado e o calandrado. O vidro flotado, que representa máis do 90 % da produción total de vidro na actualidade, é o material de construción básico do vidro arquitectónico mundial. O proceso de produción de vidro flotado fundouse en 1952 e estableceu o estándar mundial para a produción de vidro de alta calidade. O proceso do vidro flotado inclúe cinco pasos principais:
● ingredientes
● fusión
● conformación e revestimento
● recocido
● corte e embalaxe
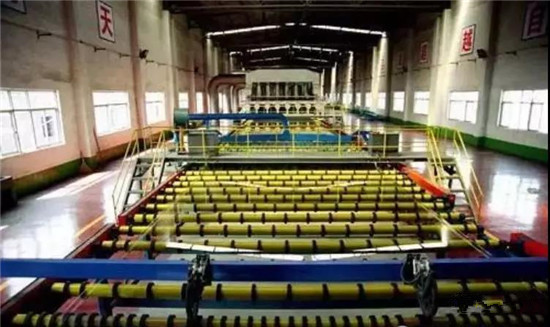
Ingredientes
A dosificación é a primeira etapa, que prepara as materias primas para a fusión. As materias primas inclúen area, dolomita, calcaria, carbonato de sodio e mirabilita, que se transportan en camión ou tren. Estas materias primas almacénanse na sala de dosificación. Hai silos, tolvas, cintas transportadoras, canaletas, colectores de po e os sistemas de control necesarios na sala de materiais, que controlan o transporte de materias primas e a mestura dos materiais da mestura. Desde o momento en que as materias primas se entregan á sala de materiais, están en constante movemento.
Dentro da sala de dosificación, unha cinta transportadora longa e plana transporta continuamente as materias primas desde os silos de diversas materias primas ata o elevador de cangilóns capa por capa en orde, e despois envíaas ao dispositivo de pesaxe para comprobar o seu peso composto. A estes ingredientes engadiranse fragmentos de vidro reciclado ou retornos da liña de produción. Cada lote contén aproximadamente un 10-30 % de vidro roto. Os materiais secos engádense ao mesturador e mestúranse co lote. O lote mesturado envíase desde a sala de dosificación ao silo da cabeza do forno para o seu almacenamento a través da cinta transportadora e, a continuación, engádese ao forno a unha velocidade controlada polo alimentador.

Composición típica do vidro
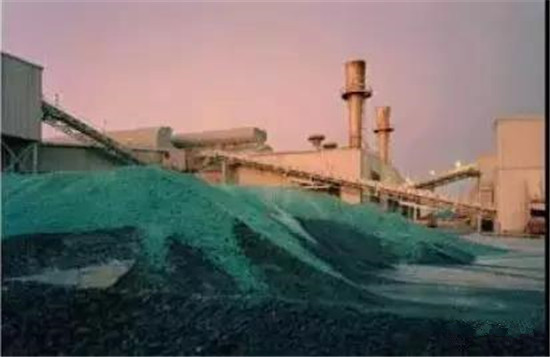
Patio de residuos de madeira
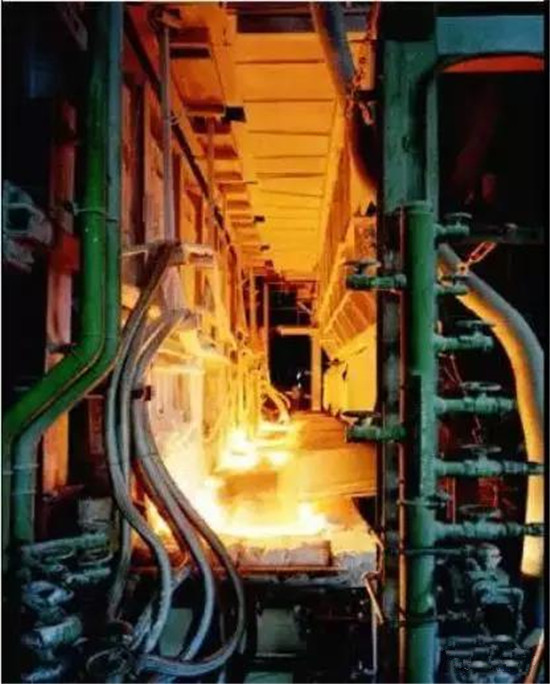
Introduza as materias primas mesturadas na entrada do forno ata 1650 graos cunha tolva
Fusión
Un forno típico é un forno de chama transversal con seis rexeneradores, duns 25 metros de ancho e 62 metros de ancho, cunha capacidade de produción diaria de 500 toneladas. As partes principais do forno son a piscina de fusión/clarificador, a piscina de traballo, o rexenerador e o pequeno forno. Como se mostra na Figura 4, está feito de materiais refractarios especiais e ten unha estrutura de aceiro no marco exterior. O lote envíase á piscina de fusión do forno polo alimentador, e a piscina de fusión quéntase a 1650 ℃ mediante a pistola pulverizadora de gas natural.
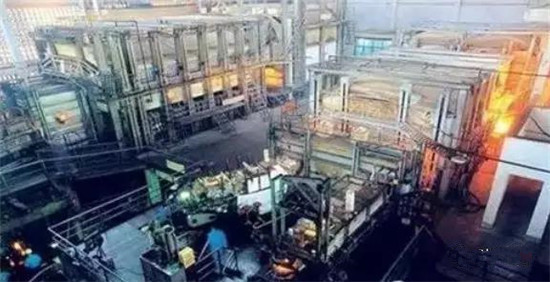
O vidro fundido flúe desde a piscina de fusión ata a zona do pescozo a través do clarificador e axítase uniformemente. Despois, flúe cara á parte de traballo e arrefría lentamente ata uns 1100 graos para alcanzar a viscosidade correcta antes de chegar ao baño de estaño.
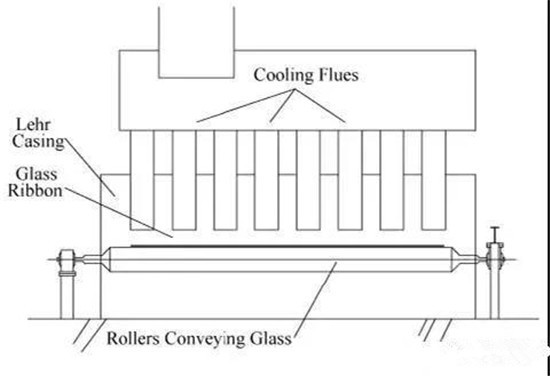
Formación e revestimento
O proceso de formación do vidro líquido clarificado nunha placa de vidro é un proceso de manipulación mecánica segundo a tendencia natural do material, e o grosor natural deste material é de 6,88 mm. O vidro líquido sae do forno a través da zona do canal e o seu fluxo contrólase mediante unha porta axustable chamada pistón, que se atopa a uns ± 0,15 mm de profundidade no vidro líquido. Flota sobre o estaño fundido, de aí o nome de vidro flotado. O vidro e o estaño non reaccionan entre si e pódense separar; a súa resistencia mutua en forma molecular fai que o vidro sexa máis liso.
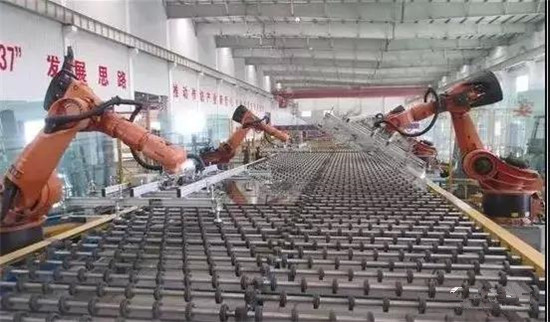
O baño é unha unidade selada nunha atmosfera controlada de nitróxeno e hidróxeno. Inclúe aceiro de soporte, carcasas superior e inferior, refractarios, estaño e elementos calefactores, atmosfera redutora, sensores de temperatura, sistema de control de procesos informático, uns 8 metros de ancho e 60 metros de longo, e a velocidade da liña de produción pode alcanzar os 25 metros/minuto. O baño de estaño contén case 200 toneladas de estaño puro, cunha temperatura media de 800 ℃. Cando o vidro forma unha capa fina ao final da entrada do baño de estaño, chámase placa de vidro, e unha serie de tiradores de bordos axustables funcionan en ambos os dous lados. O operador usa o programa de control para axustar a velocidade do forno de recocido e da máquina de debuxo de bordos. O grosor da placa de vidro pode estar entre 0,55 e 25 mm. O elemento calefactor da partición superior úsase para controlar a temperatura do vidro. A medida que a placa de vidro flúe continuamente a través do baño de estaño, a temperatura da placa de vidro baixará gradualmente, facendo que o vidro sexa plano e paralelo. Neste punto, pódese usar acuracoat® para o revestimento en liña de película reflectante, película de baixa emisividade, película de control solar, película fotovoltaica e película autolimpante en equipos de CVD de pirólise. Neste momento, o vidro está listo para arrefriar.
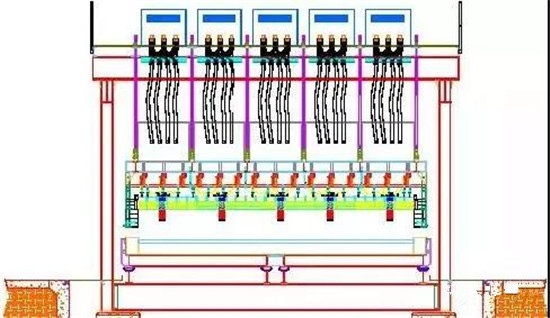
Sección transversal do baño
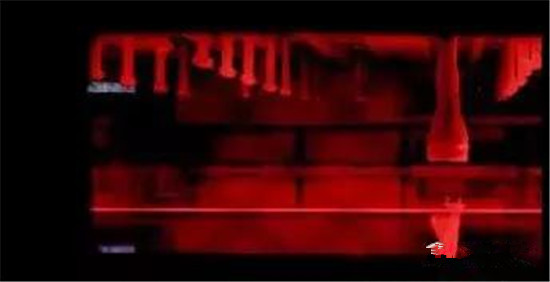
O vidro esténdese nunha capa fina sobre o estaño fundido, mantense separado del e fórmase nunha placa
O elemento calefactor colgante proporciona subministración de calor e a anchura e o grosor do vidro contrólanse mediante a velocidade e o ángulo do extractor de bordos.
Recocido
Cando o vidro formado sae do baño de estaño, a temperatura do vidro é de 600 ℃. Se a placa de vidro se arrefría na atmosfera, a superficie do vidro arrefriarase máis rápido que o interior do vidro, o que provocará unha compresión grave da superficie e unha tensión interna nociva da placa de vidro.
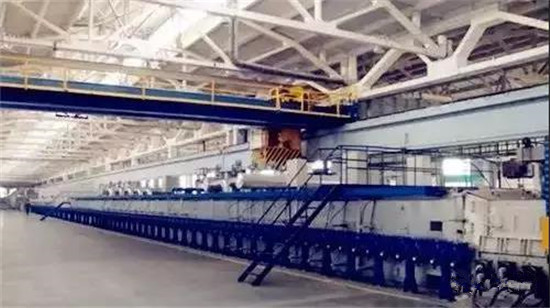
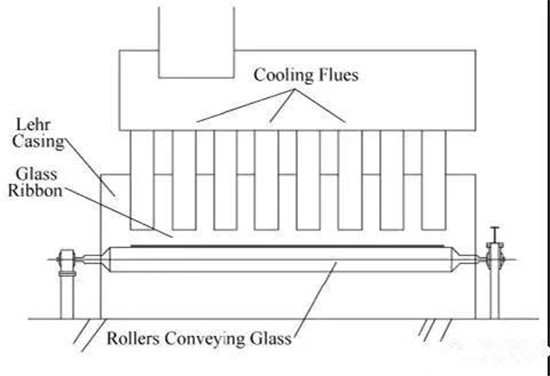
Sección do forno de recocido
O proceso de quecemento do vidro antes e despois do moldeo é tamén o proceso de formación de tensión interna. Polo tanto, é necesario controlar a calor para reducir gradualmente a temperatura do vidro á temperatura ambiente, é dicir, o recocido. De feito, o recocido lévase a cabo nun forno de recocido con gradiente de temperatura preestablecido (véxase a Figura 7) duns 6 metros de ancho e 120 metros de longo. O forno de recocido inclúe elementos de calefacción e ventiladores controlados electricamente para manter estable a distribución transversal da temperatura das placas de vidro.
O resultado do proceso de recocido é que o vidro se arrefría coidadosamente á temperatura ambiente sen tensións nin esforzos temporais.
Corte e envasado
As placas de vidro arrefriadas polo forno de recocido transpórtanse á zona de corte a través da mesa de rolos conectada ao sistema de accionamento do forno de recocido. O vidro pasa polo sistema de inspección en liña para eliminar calquera defecto e córtase cunha roda de corte de diamante para eliminar o bordo do vidro (o material do bordo recíclase como vidro roto). Despois, córtase ao tamaño requirido polo cliente. A superficie do vidro espolvorease con medio en po, de xeito que as placas de vidro se poidan apilar e almacenar para evitar que se peguen ou se raien. Despois, as placas de vidro impecables divídense en pilas para o seu embalaxe mediante máquinas manuais ou automáticas e transfírense ao almacén para o seu almacenamento ou envío aos clientes.
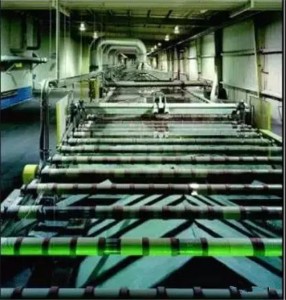
Despois de que a placa de vidro saia do forno de recocido, a placa de vidro fórmase completamente e móvese á zona de arrefriamento para continuar a reducir a temperatura.